Las granalladoras se caracterizan por ser equipos sometidos a un desgaste permanente. Cuando se detecta abrasión en cualquiera de los componentes, este debe ser reemplazado de forma inmediata para no comprometer el buen funcionamiento de la granalladora.
Por lo tanto, la única forma de asegurar el perfecto estado del equipo es mediante un programa de mantenimiento preventivo.
Además, esto ayudará a no malgastar dinero evitando paradas de producción e incluso costes de reparación.
El mantenimiento preventivo, clave para las granalladoras
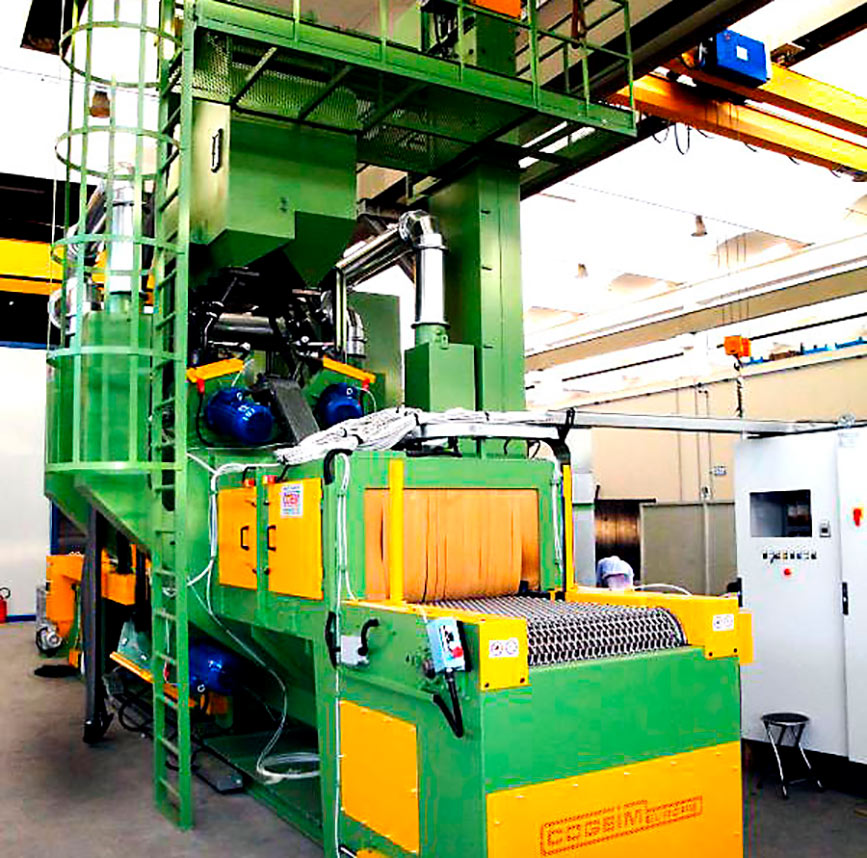
En la mayoría de los casos, las roturas prematuras tanto de pequeños componentes como de máquinas enteras, se derivan de no haber sustituido pequeñas piezas a tiempo. Otras consecuencias son el consumo alto de abrasivo y procesos de producción que se alargan más de lo previsto, generando costes adicionales.
Gracias al mantenimiento preventivo se consigue programar el chequeo o testeo periódico de los componentes que suelen fallar más a menudo. Esto también conlleva otras tareas como la adición de aceites o taladrinas cuando sea necesario.
¿Sobre quién recae la responsabilidad de este mantenimiento? Cada empresa debe especificar a sus trabajadores este punto. No obstante, nuestro equipo de profesionales recomienda que tanto el trabajador como el encargado de mantenimiento se ocupen de estas labores.
Está claro que para obtener resultados satisfactorios la empresa también debe poner de su parte. Por ejemplo, se espera que lleve a cabo las siguientes tareas:
- Entrenar a los trabajadores y darles las herramientas y otros recursos necesarios para que efectúen el mantenimiento de granalladoras dentro del marco de la seguridad laboral.
- Detallar de forma estadística los tiempos en el proceso, cantidad de piezas producidas, consumo de granalla, etc.
- Prevenir el espacio de la presencia de polvo que podría saturar los filtros del colector.
Si todos estos aspectos se llevan a cabo, la inversión en granalladoras será mucho más rentable y estas alargarán su vida útil con toda seguridad.